DIGITAL TWIN
Applications and advantages
Manufacturing
- Designing and testing of product
- Material selection
- Customizing the products
- Optimizing production planning and control
- Layout/Floor planning
- Predicting maintenance issues and developing a maintenance strategy
- Real-time monitoring of production and service
- Remote troubleshooting of equipment
- Analyzing and forecasting energy consumption
- Analyzing user behavior
- Recovering the waste
- Validation tool for HRC safety standards
- Collaboration tool
- Better-designed products
- Fewer design iterations
- Faster and cheaper production
- Increases reliability of equipment and production lines
- Reduces downtime
- Improves decision support
- Lower maintenance costs
- Less wastage
Mining
- Process/operation optimization
- Predictive maintenance of assets
- Predicting and optimizing transport network
- Simulating and analyzing different scenarios across value chain
- Trains new miners, especially for emergency situations
- Improves asset and transportation reliability
- Cuts down unplanned downtime
- Improves processes’ efficiency and product quality
- Risk-free and stress-free environment
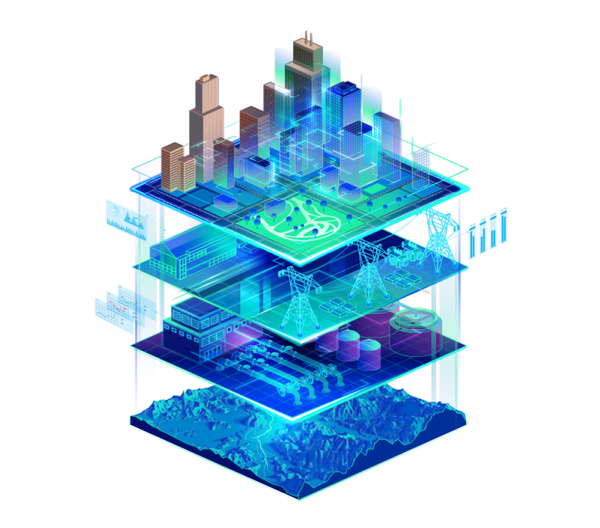
Companies have a prime opportunity to optimize and maximize returns in their manufacturing operations by leveraging the extensive capabilities of the Digital Twin Technology.
The future of digital twins is nearly limitless, due to the fact that increasing amounts of cognitive power are constantly being devoted to their use. So digital twins are constantly learning new skills and capabilities, which means they can continue to generate the insights needed to make products better and processes more efficient.